Company News
6082 aluminium deoxidation hot rolling wire rod
Editor :frank
Time :2019-11-21 16:25
6082 aluminum wire rod is the most commonly used deoxidizer in modern steelmaking and production. The role of aluminum wire in steel mainly includes: calming molten steel to prevent bubbles from forming when molten steel solidifies; forming dispersed AlN particles, fixing nitrogen in steel, controlling austenite grain size when steel is reheated, and increasing grain size Roughening temperature, reducing the superheat sensitivity and hardenability of steel, improving the welding performance of steel; suppressing the aging characteristics of low carbon steel; reducing the notch sensitivity and ductile-brittle transition temperature of steel.
6082 aluminium hot rolling wire rod manufacture Mechanical properties:
Tensile strength σb (MPa): ≥ 205
Conditional yield strength σ0.2 (MPa): ≥110
Length ratio δ10 (%): ≥14
Note: Longitudinal mechanical properties of profiles at room temperature Specimen size: all thicknesses
Homogenization temperature: 555-565 ° C holding time: 3 hours, cooling rate ≥ 200 ° C /
6082 aluminium deoxidation wire rod supplier Heat treatment process:
1. Melting 6082 alloy is characterized by containing Mn, Mn is a refractory metal, and the melting temperature should be controlled at 740-760 °C. Stir twice or more before sampling to ensure complete melting of the metal, accurate temperature and uniform composition. After stirring, take a sample in the middle of the depth of the aluminum liquid and the left and right sides of the furnace for analysis.
2. Purification and casting After the melt is transferred to the static furnace, it is sprayed with powder and jet refining with nitrogen and refining agent. The refining temperature is 735-745 ° C for 15 minutes, and it is allowed to stand for 30 minutes after refining. Through this process, the gas is removed, the slag is removed, and the melt is purified. During the casting, there are two filtering devices between the mold and the furnace mouth. The furnace mouth is filtered by a ceramic foam filter plate (30PPI). Before casting, it is filtered with 14 mesh glass fiber cloth to fully filter the oxide and slag in the melt.
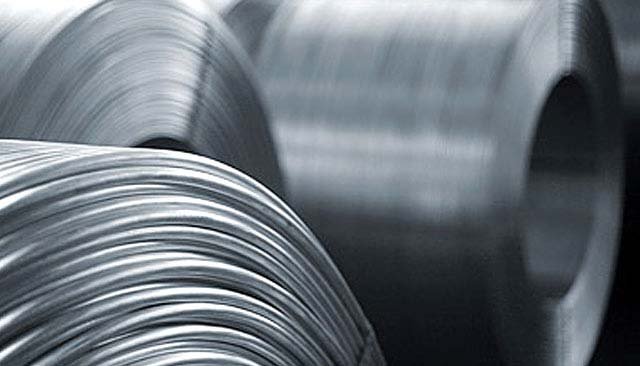
6082 aluminium hot rolling wire rod manufacture Mechanical properties:
Tensile strength σb (MPa): ≥ 205
Conditional yield strength σ0.2 (MPa): ≥110
Length ratio δ10 (%): ≥14
Note: Longitudinal mechanical properties of profiles at room temperature Specimen size: all thicknesses
Homogenization temperature: 555-565 ° C holding time: 3 hours, cooling rate ≥ 200 ° C /
6082 aluminium deoxidation wire rod supplier Heat treatment process:
1. Melting 6082 alloy is characterized by containing Mn, Mn is a refractory metal, and the melting temperature should be controlled at 740-760 °C. Stir twice or more before sampling to ensure complete melting of the metal, accurate temperature and uniform composition. After stirring, take a sample in the middle of the depth of the aluminum liquid and the left and right sides of the furnace for analysis.
2. Purification and casting After the melt is transferred to the static furnace, it is sprayed with powder and jet refining with nitrogen and refining agent. The refining temperature is 735-745 ° C for 15 minutes, and it is allowed to stand for 30 minutes after refining. Through this process, the gas is removed, the slag is removed, and the melt is purified. During the casting, there are two filtering devices between the mold and the furnace mouth. The furnace mouth is filtered by a ceramic foam filter plate (30PPI). Before casting, it is filtered with 14 mesh glass fiber cloth to fully filter the oxide and slag in the melt.
Previous :5154 aluminum-magnesium alloy wire rod
Next :aluminum shots particle
Related :
- 180 Grade Self Bonding Enamelled aluminium Wire2013.12.19
- 1050 1350 Bunched Aluminium Wire2013.12.19
- Industrial Pure Cold Drawn Aluminium Wire Cable 1352013.12.19
- Deoxidized round aluminum rods2013.12.19
- The role and practical application of coiled alumin2013.12.19